Glass sandblasting is a popular method used in creating custom designs on glass surfaces. It involves the use of high-pressure air mixed with sand particles to etch designs onto the surface of the glass. This technique is lauded for its versatility and the unique, frosted appearance it lends to the glass. However, like any process, it is not without its drawbacks. This article aims to delve into the limitations of glass sandblasting, particularly in the context of custom design.
The first aspect we will explore is the precision and complexity limitations of custom design in glass sandblasting. While sandblasting can create beautiful designs, there are restrictions in the level of detail and complexity achievable due to the nature of the process. Next, we will discuss the impact of material thickness and pressure on glass sandblasting. The thickness of the glass and the pressure used during sandblasting can significantly affect the outcome, presenting certain challenges that need careful consideration.
The article will then shift focus to the challenges with durability and longevity in glass sandblasting. Despite the stunning results initially, the durability of sandblasted glass designs can be a concern over time. Health and safety are also critical aspects to consider in any process, and sandblasting is no exception. We will examine the potential health and safety risks associated with the process, and ways these can be mitigated.
Finally, we will look at the limitations of equipment and technology in glass sandblasting. While technology advancements have improved the process, there are still limitations that can affect the overall design and execution of the sandblasting. Each of these topics will shed light on the constraints of glass sandblasting in custom design, providing a comprehensive understanding of the process and its limitations.
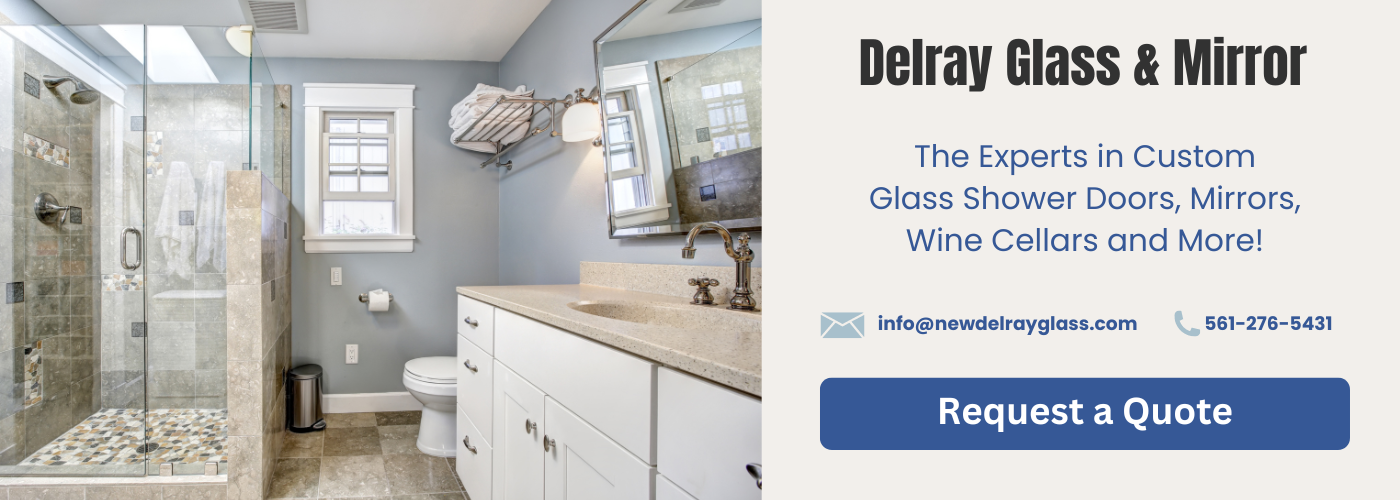
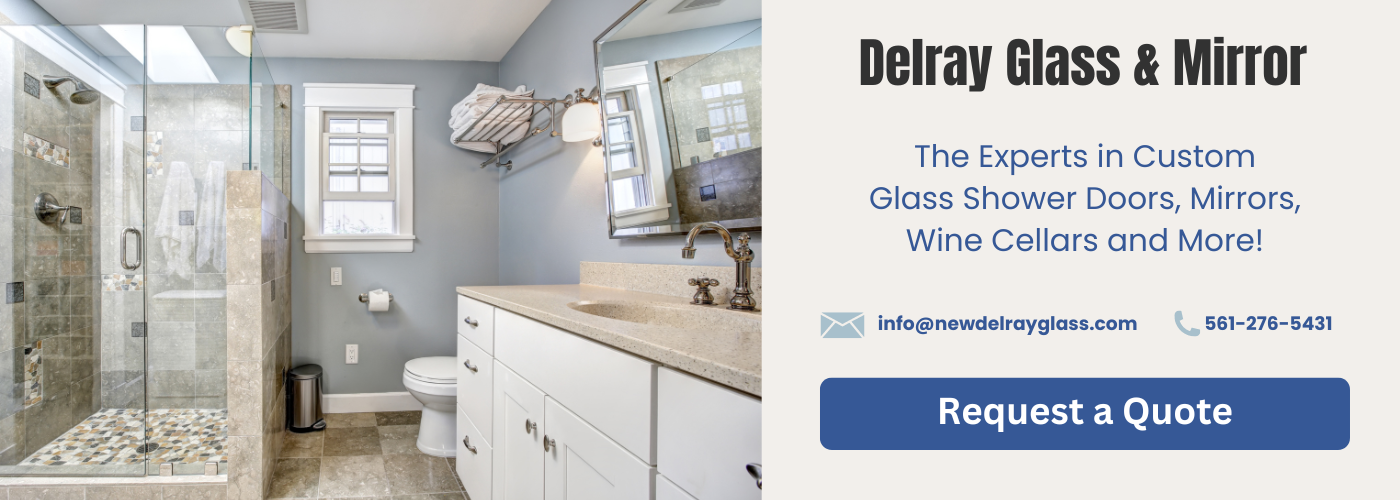
The Precision and Complexity Limitations of Custom Design in Glass Sandblasting
The Precision and Complexity Limitations of Custom Design in Glass Sandblasting is one of the significant limitations in the field of glass sandblasting. Sandblasting is a common technique used to etch or carve designs into glass. Despite its popularity, it has some limitations, especially when it comes to precision and complexity of the design.
The process of sandblasting involves shooting a stream of abrasive material, such as sand, at high speed against the glass surface. This abrasive action erodes the glass surface to create the desired design. However, the very nature of this process might not allow for precise and intricate designs. The sandblasting process is relatively aggressive and could lead to a loss of detail in the design. Thus, if a design requires sharp, fine lines or elaborate details, sandblasting might not be the best method to use.
Furthermore, the complexity limitation is also a major concern. With sandblasting, it is difficult to achieve highly complex designs. The process is more suitable for simple and less detailed designs. More complex designs would require more sophisticated techniques and equipment. This is because complex designs often involve varying depths and gradients which are hard to achieve with a process as rudimentary as sandblasting.
In conclusion, while sandblasting is an effective method to etch designs into glass, it does have its limitations, particularly in terms of precision and complexity. These limitations can restrict the creativity and flexibility of artists and designers who wish to use this technique. Therefore, alternative methods should be considered for designs that require a high level of detail or complexity.
The Impact of Material Thickness and Pressure on Glass Sandblasting
The process of glass sandblasting is greatly affected by the thickness of the glass material and the pressure applied. These two factors can significantly limit the custom designs that can be achieved through sandblasting.
The thickness of the glass plays a crucial role in determining the final output. Thin glass may not withstand high-pressure sandblasting, leading to breakage. On the other hand, extremely thick glass may require high-pressure sandblasting which can lead to uneven results. Therefore, determining the right thickness of glass for sandblasting is critical to achieving desired results.
Pressure is another integral factor. Too little pressure may not etch the glass effectively, while too much pressure can cause the glass to crack. Moreover, improper pressure control can lead to inconsistent patterns on the glass surface. This limitation can restrict the complexity and detailing of the designs that can be created through sandblasting.
In conclusion, while glass sandblasting is a popular method for creating custom designs, the impact of material thickness and pressure can pose significant limitations. It requires a careful balance of these factors to achieve the desired design without damaging the material. Despite these challenges, with the right combination of glass thickness and pressure, beautiful and intricate designs can be achieved through this process.
The Challenges with Durability and Longevity in Glass Sandblasting
Glass sandblasting is a popular method for etching designs into glass surfaces. It involves the use of high-pressure air mixed with sand or another abrasive material to chip away at the surface of the glass. One of the limitations of this process, especially when it comes to custom designs, is the issue of durability and longevity.
For starters, the sandblasting process inherently weakens the glass. The process of chipping away at the glass surface causes microscopic cracks and fissures, which can make the glass more prone to breaking over time. This is particularly a concern for pieces that will be regularly handled or exposed to the elements.
Moreover, the design itself can also affect the durability of the piece. Complex designs with many fine details can be more fragile than simpler ones, as the glass in these areas may be thinner and therefore more prone to damage. Over time, these designs can also wear away or become less distinct, particularly if the piece is cleaned regularly or exposed to harsh environmental conditions.
Finally, the type of glass and the quality of the sandblasting work can also play a role in the longevity of the piece. Certain types of glass are more resilient than others, and a professional sandblaster will be able to adjust their technique to suit the material. However, even with the best materials and technique, the inherent limitations of the sandblasting process can still pose challenges for the durability and longevity of custom designs.
In conclusion, while glass sandblasting can create beautiful custom designs, factors such as the inherent weakening of the glass, the complexity of the design, and the quality of the work can all impact the durability and longevity of the final product. Thus, it’s important to consider these limitations when deciding on a custom design.
Health and Safety Concerns in Glass Sandblasting Process
When discussing the limitations of glass sandblasting in custom design, it’s crucial to consider health and safety concerns associated with the process. This aspect, while not directly influencing the design outcome, is nonetheless a significant consideration that can impact the overall execution and efficiency of the project.
The process of sandblasting involves the use of small, abrasive particles that are propelled at high speeds to etch or clean a glass surface. This can pose a risk of injury to workers if not properly managed. For instance, the particles can cause skin and eye injuries if appropriate protective gear is not worn. Moreover, the dust generated during the process can lead to respiratory problems if inhaled over prolonged periods.
In addition to physical health risks, there are also potential safety hazards in the workplace. The equipment used in sandblasting can be dangerous if not handled correctly. This includes high-pressure hoses that can cause injury or damage if they malfunction or are mishandled. Furthermore, the noise generated during the process can also pose a risk to workers’ hearing health.
From a broader perspective, these health and safety concerns can limit the efficiency and effectiveness of the glass sandblasting process. They necessitate rigorous training and strict safety protocols, which can add to the time, cost, and complexity of the project. Therefore, while these concerns may not directly impact the design outcome, they remain a significant limitation in the overall process of glass sandblasting in custom design.
The Limitations of Equipment and Technology in Glass Sandblasting
The limitations of equipment and technology in glass sandblasting are a significant consideration when it comes to custom design. The process of sandblasting involves the use of specific machinery to forcibly propel a stream of abrasive material against a surface. The equipment used has a significant bearing on the quality and precision of the end result.
One of the primary limitations is the inherent difficulty in achieving intricate designs with conventional sandblasting equipment. The abrasive stream is difficult to control with absolute precision, which often leads to a lack of fine detail or unevenness in the finished product. This lack of control can be particularly problematic when working on custom designs, which often require a high degree of precision and detail.
Moreover, the technology available in the field of glass sandblasting is not as advanced as that in some other areas of custom design. This implies that there are constraints on the level of sophistication and complexity that can be achieved in the designs. This is not to say that intricate designs are impossible, but they require a higher degree of skill and experience to execute successfully.
Another limitation arises from the wear and tear on the equipment. The abrasive nature of sandblasting means that the equipment used is subject to significant wear and tear, which can affect the consistency and quality of the finished product over time. Regular maintenance and replacement of parts is therefore essential, but this can be costly and time-consuming.
In summary, while glass sandblasting is a powerful tool for creating custom designs, it is not without its limitations. The equipment and technology available present certain challenges in terms of the level of detail that can be achieved and the consistency of the finished product. However, with skilled operators and regular maintenance, these limitations can be mitigated to some extent.