Sandblasting, a versatile process used across various industries, plays a significant role in the world of glasswork. This technique employs a range of specialized equipment to etch, carve, or create a frosted look on glass surfaces. Glass sandblasting is a nuanced method that necessitates keen understanding and precision, in addition to the right tools and machinery. The type of equipment used for glass sandblasting can range from small handheld tools to larger industrial machines. This article aims to provide an in-depth insight into the different types of glass sandblasting equipment, their functioning and mechanisms, safety equipment used, maintenance and care tips, and the latest innovations and technological advancements in the field.
The first section, “Different Types of Glass Sandblasting Equipment,” will delve into the various tools and machines used in the process. From simple handheld devices to larger, more complex machinery, this section will provide a comprehensive overview of the equipment that forms the backbone of the sandblasting process.
Next, we will explore “The Functioning and Mechanism of Glass Sandblasting Machines.” Understanding how these machines work and the principles behind sandblasting can be crucial to achieving the desired results.
Safety should always be a priority in any industrial process, and sandblasting is no exception. In “Safety Equipment Used in Glass Sandblasting,” we will discuss the protective gear necessary to ensure the well-being of workers involved in the sandblasting process.
Maintenance and care for these machines is as important as understanding their operation. In “Maintenance and Care for Glass Sandblasting Equipment,” the article will provide useful tips and guidelines for keeping your equipment in optimal condition, thus prolonging its life and efficiency.
Finally, we wrap up with a look at the future in “Innovations and Technological Advancements in Glass Sandblasting Equipment.” This section will shed light on the latest developments in sandblasting equipment, giving readers a glimpse into the future of this fascinating process. From automation to AI, the world of glass sandblasting is evolving, and this article aims to keep you at the forefront of these changes.
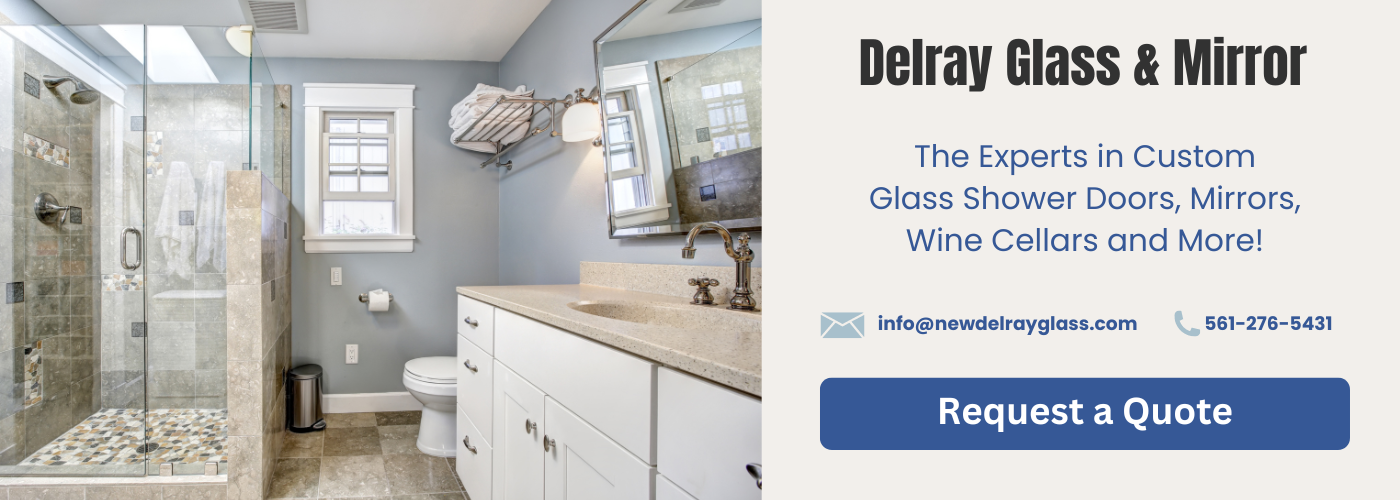
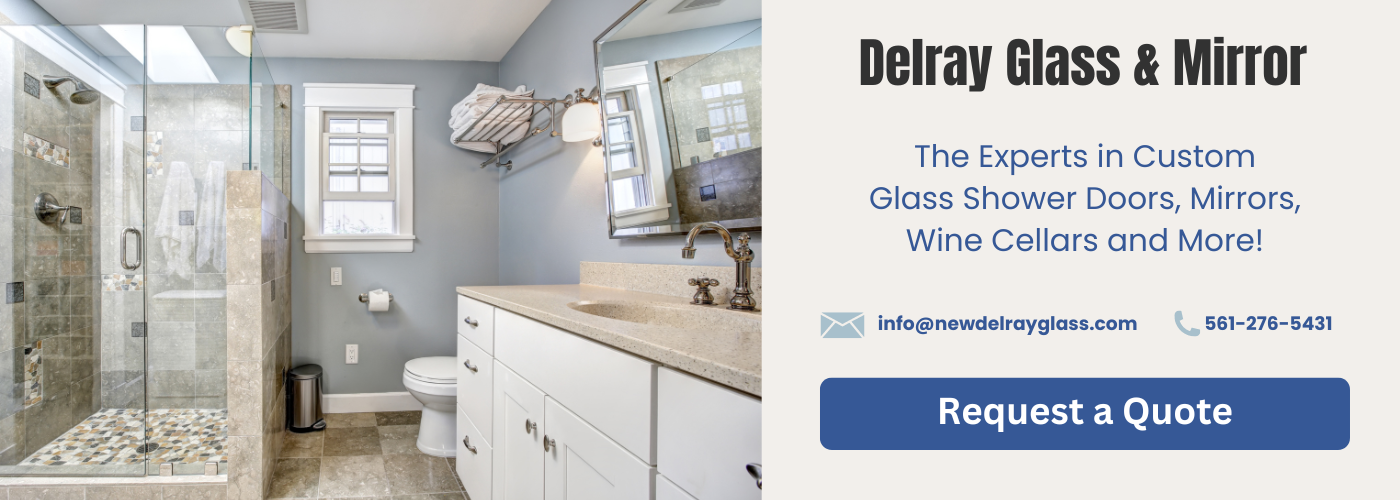
Different Types of Glass Sandblasting Equipment
Sandblasting, also known as abrasive blasting, is a method used to smooth, roughen or clean surfaces. When it comes to glass, sandblasting is used for etching or frosting the glass to create beautiful designs or to obscure visibility. To achieve this, different types of equipment are used, each with its unique functionalities.
The first type of equipment used in glass sandblasting is the sandblasting cabinet. This enclosed unit is designed to prevent the escape of abrasive materials, making it safe for the user and the environment. It has a viewing glass for the operator to see the work process. The cabinet can either be a suction or pressure system. In a suction system, the gun sucks the abrasive materials and fires it onto the glass surface. On the other hand, a pressure system uses compressed air to push the abrasive materials onto the glass surface, which is faster and more aggressive than the suction system.
The second type is the portable sandblasting equipment. This equipment is typically used for large glass surfaces or outdoor projects. It is not enclosed like the cabinet and requires the operator to use protective gear.
Another type is the dustless sandblasting equipment. This type of equipment mixes water with the abrasive materials to reduce dust production. It’s environmentally friendly and reduces cleanup efforts.
The last but not least is the specialized glass sandblasting equipment. This equipment offers precision and is often used for creating detailed designs on the glass. It uses specialized nozzles and abrasive materials to achieve the desired effect.
Each of these types of glass sandblasting equipment has its unique pros and cons. Therefore, the choice of equipment depends on the specific requirements of the project and the skill level of the operator.
The Functioning and Mechanism of Glass Sandblasting Machines
Glass sandblasting is a technique used for creating designs and patterns on the surface of a glass. The machine used for this purpose is termed as a glass sandblasting machine. It functions by using air pressure to force abrasive materials against the glass surface, which in turn creates the desired effect.
The functioning and mechanism of glass sandblasting machines are quite complex. These machines utilize a system that involves a compressor, a blasting tank, and an abrasive material. The compressor creates pressurized air, which is then fed into the blasting tank. This tank is filled with the abrasive material, usually sand, which is propelled out of the tank and onto the glass surface when the pressurized air is released.
The abrasive material impacts the glass surface, chipping away tiny particles and creating a frosted or etched appearance. Depending upon the type of sandblasting machine, the operator can control the air pressure, the type of abrasive used, and the pattern being created.
The mechanism of glass sandblasting machines allows for a high level of precision and detail. The operator can easily control the depth and pattern of the etching, which makes it possible to create intricate designs and logos. Furthermore, different types of abrasive materials can be used for different effects, adding to the versatility of these machines.
To summarize, the functioning and mechanism of glass sandblasting machines involve the use of air pressure and abrasive materials to create designs and patterns on the surface of the glass. This process requires a high level of precision and control, making it a highly skilled craft.
Safety Equipment Used in Glass Sandblasting
Safety equipment forms an integral part of any glass sandblasting process. This equipment is designed to ensure the safety of the operator and other individuals in the vicinity during the operation. Glass sandblasting entails the use of high-pressure machinery to etch or clean glass. This process generates a substantial amount of dust and debris that can be harmful if inhaled or come into contact with the skin or eyes.
The most basic piece of safety equipment is a good quality sandblasting helmet. This helmet is designed to protect the operator’s head, face, and especially the eyes from flying debris. It often comes equipped with a ventilation system to provide a continuous supply of fresh air, therefore preventing the inhalation of harmful dust particles.
In addition to the helmet, operators should also wear a heavy-duty blast suit. These suits are made from durable materials designed to resist abrasion and protect the wearer from the high-speed impact of the sand particles. They also cover the entire body, thereby providing comprehensive protection.
Gloves are another key element of safety equipment. These gloves are usually made of heavy-duty leather or other robust materials to protect the hands from abrasion and cuts. They should be long enough to overlap with the sleeves of the blast suit, ensuring no skin is exposed.
Lastly, safety boots are also essential. These boots are typically steel-toed to protect the feet from any heavy falling objects and have a thick sole to prevent injury from any sharp debris on the floor.
While the glass sandblasting equipment performs the task, the safety equipment protects the operator. Therefore, both are equally important for an efficient and safe sandblasting process. The use of safety equipment not only ensures the physical well-being of the operator but also enhances productivity by reducing the possibilities of injuries and consequent downtime.
Maintenance and Care for Glass Sandblasting Equipment
Maintaining and taking care of your glass sandblasting equipment is essential in ensuring its longevity and efficiency. Regular maintenance not only keeps the machinery working at its best, but it also helps to prevent accidents or potential damage that might occur due to faulty or worn-out parts.
The process of maintaining glass sandblasting equipment often involves regular inspections and cleaning. Inspections should be thorough, covering all parts of the machine, including the blasting cabinet, blasting gun, and air compressor. Any signs of wear or damage, such as cracks, leaks, or excessive dust buildup, should be immediately addressed.
Cleaning, on the other hand, should focus on removing any dust or debris from the machine. This includes emptying the dust collector, cleaning the blasting cabinet, and ensuring the air compressor is free of dirt and dust.
Proper care for glass sandblasting equipment also includes using the right type of abrasive. Using an abrasive that is too harsh can damage the equipment, while one that is too mild may not provide the desired results.
Lastly, when not in use, the equipment should be stored in a clean and dry place to prevent rust and other forms of damage. Performing these maintenance tasks regularly will ensure that your glass sandblasting equipment remains in good working condition for a long time.
Innovations and Technological Advancements in Glass Sandblasting Equipment
The field of glass sandblasting has witnessed multiple innovations and technological advancements in recent years, enhancing the overall efficiency and precision of the process. The introduction of computerized systems, for instance, has revolutionized the operations of glass sandblasting equipment. These systems allow for greater control over the sandblasting process, enabling the creation of intricate designs on glass surfaces.
Automated sandblasting equipment is another significant advancement. These machines offer high-speed performance and are capable of sandblasting large areas in a short period. They reduce the need for manual labor, making the process more cost-effective and less time-consuming. The automation of sandblasting equipment has also improved the consistency and quality of the finished glass products.
Moreover, the development of environmentally friendly sandblasting equipment marks another crucial innovation. Such machines use biodegradable materials for sandblasting, reducing the environmental impact of the process.
Lastly, the advancements in safety features of glass sandblasting equipment have also been noteworthy. Modern machines come equipped with advanced safety features like auto-shutoff and protective casing to prevent accidents and ensure the safety of the operator. These technological advancements and innovations have indeed played a significant role in enhancing the capabilities of glass sandblasting equipment, making it more efficient, safe, and eco-friendly.